Расчет Коробки Скоростей
Шпаргалка: Расчет коробки скоростей. Выбор задания. Выбор и обоснование кинематической схемы станка. Определение частот вращения выходного вала (шпинделя). Построение кинематической схемы сложной коробки скоростей7. Построение структурной сетки.12. Анализ структурной сетки13. Sep 18, 2010 - Кинематический расчет коробки скоростей горизонтально-фрезерного станка. Выбор предельных режимов резания.
Регулирование скоростей (в данном диапазоне) может быть ступенчатым и бесступенчатым. Современные станки общего назначения в большинстве случаев имеют ступенчатое регулирование частот вращения шпинделя. Коробки скоростей со ступенчатым регулированием более компактны и просты, имеют высокий. Частоты вращения шпинделя распределяются по геометрическому ряду, что позволяет обеспечивать постоянный перепад скоростей, а также дает возможность проектировать сложные коробки скоростей, состоящие из элементарных двухваловых передач, также построенных по геометрическому ряду. Геометрический ряд частот вращения имеет следующие стандартные значения: 1,06; 1,12; 1,26; 1,41; I,58; 1,78; 2,00 Они имеют следующую область применения: φ=1,06 имеет вспомогательное значение; φ=1,12 применяется в автоматах, где требуется более точная настройка на заданный режим; φ=1,26 и 1,41 основные ряды в универсальных станках; φ=1,58 и 1,78 применяются в станках, где время обработки невелико по сравнению со временем холостых ходов; φ=2,00 применяется редко и имеет вспомогательное значение при расчете промежуточных множительных коробок скоростей. Число ступеней частот вращения шпинделя определяется по формуле: (6) Расчетное число ступеней частот вращения шпинделя можно округлить до стандартного значения: 4; 6; 8; 9; 12; 16; I8; 24; 36. Далее определяются промежуточные значения чисел оборотов: n 1 = nmin n 2 = n 1 φ.
Nz = nmax = n 1 φ z -1 Полученные значения промежуточных чисел оборотов шпинделя округляются, используя ГОСТ 8032-56 «Предпочтительные числа и ряды предпочтительных чисел» (см. Приложение В).
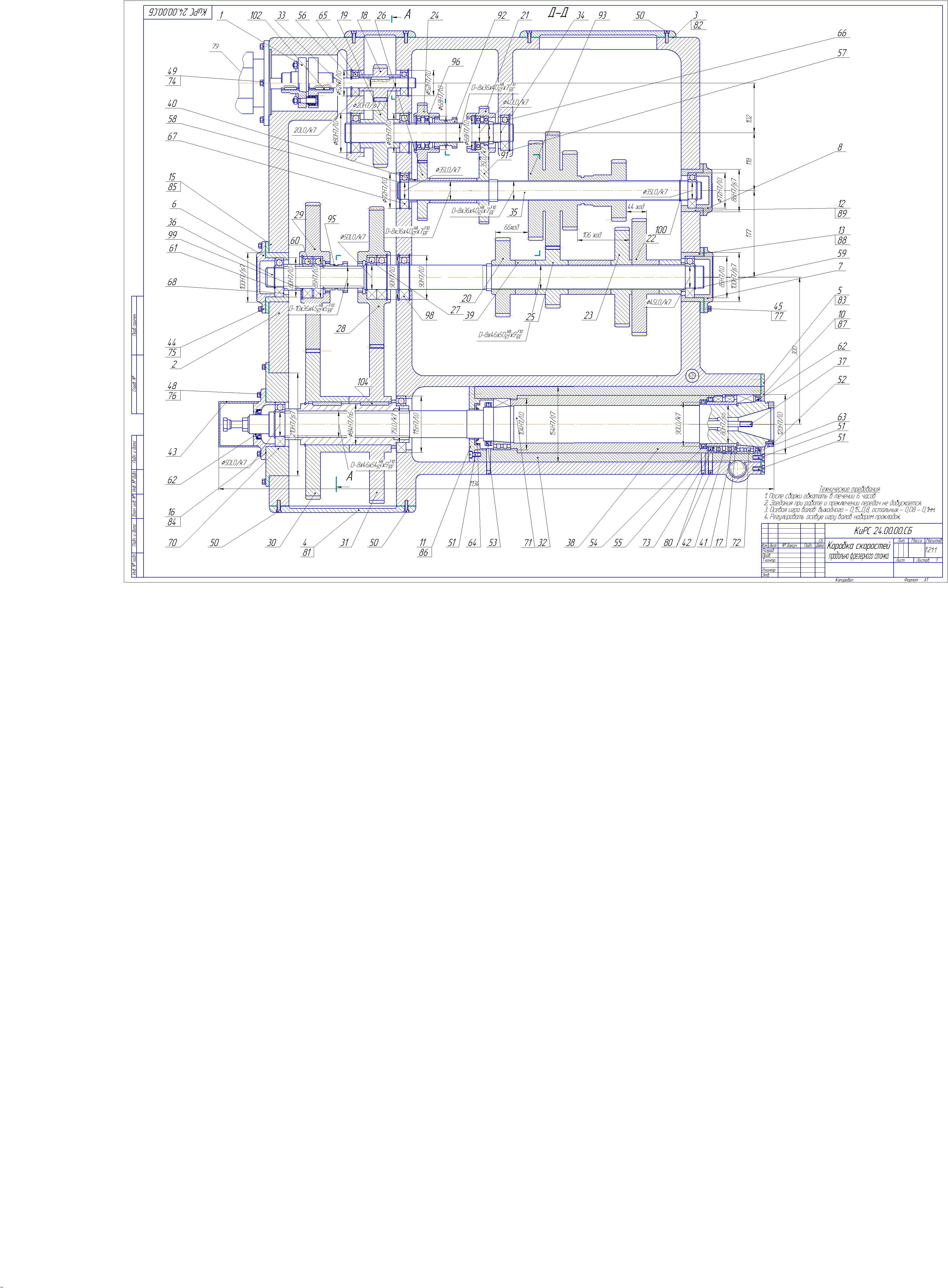
Мощность привода главного движения определяется по наибольшей эффективной мощности, необходимой для резания. Для сверлильных станков:, кВт (7) где - no число оборотов детали или инструмента об/мин:, об/мин (8) M - крутящий момент, определяемый по формуле:, Нм (9) Исходя из максимальной эффективной мощности определяют мощность электродвигателя:, кВт (10) где: η -. Привода станка, который принимается η =0,8. По мощности Nдв и наибольшей полученной частоте вращения nmax выбирается электродвигатель 6. Определение технических характеристик станков фрезерной группы При фрезеровании наибольшая и наименьшая скорости резания определяются по формулам:, (11) (12) Предельные частоты вращения шпинделя nmax и nmin определяются по формулам 3 и 4, Dmax, Dmin – предельные диаметры фрез. Диапазон регулирования частот вращения, знаменатель геометрического ряда, число ступеней частот вращения и промежуточные значения чисел оборотов определяются так же как и для станков сверлильно-расточной группы. Мощность привода главного движения определяется по наибольшей эффективной мощности, необходимой для резания.
Начинающим изучать язык рекомендуется сначала ознакомиться с комментированным текстом, а затем переходить к оригинальному. Тем же, кто уже имеет опыт чтения на иностранном языке, лучше поступать наоборот: читать текст без комментариев и подсказок, при необходимости заглядывая в адаптированный вариант для контроля понимания прочитанного. В книге текст произведения на языке оригинала повторяется дважды: сначала с лексико-грамматическим комментарием и дословным переводом некоторых фраз, затем без каких-либо подсказок. Алиса в стране чудес метод чтения ильи франка скачать.

Для фрезерных станков:, кВт (13) где тангенциальная составляющая силы резания определяется по формуле:, Н (14) где коэффициенты Ср и Кр, показатели степеней выбираются по справочнику 2; tmax - максимальная глубина фрезерования; Smax - максимальная подача, мм/об; вmax - максимальная ширина фрезерования, мм; zmax - число зубьев у фрезы с Dmax; Dmax - диаметр фрезы, мм; nmin - минимальное число оборотов шпинделя, об/мин; Исходя из максимальной эффективной мощности, определяют мощность электродвигателя:, кВт (15) где: η =0,8 –. Привода станка. По мощности Nдв и наибольшей полученной частоте вращения nmax выбирается электродвигатель 6. КВт (24) где: η =0,8 –. Привода станка.
По мощности Nдв и наибольшей полученной частоте вращения nmax выбирается электродвигатель 6. Кинематический расчет привода станка 3.2.1. Общая часть Привод главного движения металлорежущего станка состоит из коробки скоростей и электродвигателя. Преимущественное распространение в станках получили асинхронные электродвигатели, что связано с низкой их стоимостью, высокой надежностью и жесткой механической характеристикой. Регулирование скорости вращения асинхронных двигателей используют сравнительно редко и заключается оно либо за счет переключения числа пар полюсов, либо за счет изменения частоты питания.
Расчет Коробки Скоростей
Односкоростные электродвигатели используются с синхронной частотой вращения: nэ = 750, 100, 1500, 3000, многоскоростные (двухскоростные) nэ = 500/1000, 750/1500, 1500/3000, трехскоростные и четырехскоростные применяются значительно реже. Коробки скоростей в металлорежущих станках, с точки зрения их кинематической структуры, подразделяются на два вида: - коробки скоростей с множительной структурой; - коробки скоростей со сложенной структурой. Коробка скоростей с множительной структурой состоит из последовательно расположенных элементарных групповых передач. Элементарная групповая передача – это двухваловая передача на 2, 3 и 4 скорости (рис.1а, б, в). Она состоит из одной кинематической цепи. Общее число скоростей получается путем перемножения чисел скоростей элементарных двухваловых передач (2, 3 и 4 соответственно на рис. А) б) в) Рис.
1 Кинематические схемы элементарных групповых передач. Коробки скоростей со сложенной структурой строятся по принципу суммирования двух и более кинематических цепей передач, каждая из которых является множительной структурой (подробнее см.1, стр356). Кинематический расчет коробки скоростей ведется в следующей последовательности: 1. Построение структурных формул в общем и развернутом виде; 2. Построение структурных сеток и кинематической схемы; 3. Выбор наилучшего варианта структурной сетки; 4. Построение графика чисел оборотов, определение передаточных отношений и чисел зубьев; Исходными данными для расчета являются: ¾ число ступеней скорости вращения шпинделя Z; ¾ минимальная частота вращения шпинделя nmin; ¾ знаменатель геометрической прогрессии ряда φ; ¾ число оборотов электродвигателя - nэ.
Расчет Коробки Скоростей Вертикально-фрезерного Станка
Построение структурных формул в общем и развернутом виде Множительная структура привода станка состоит из последовательно включенных групп передач. Число ступеней скоростей такой структуры определяется ее структурной формулой: z= P1 × P2 × P3 × PК, (25) где z – число ступеней скорости привода; P1, P2, P3., Pk – число передач в группах, К – число элементарных групповых передач. Если в качестве привода используются двухскоростной электродвигатель, то структурная формула запишется: z= Pэ × P2 × P1 × PК, (26) где Pэ – число ступеней скоростей электродвигателя. При заданном числе ступеней частот вращения шпинделя количество групп передач, количество передач в каждой группе и порядок расположения групп может быть различным. Этот выбор, в основном, и определяет кинематику и конструкцию коробки скоростей.
Конструктивные варианты приводов для различных чисел ступеней скорости 6 8 12 16 18 24 2 3 2 2 2 3 2 2 2 3 3 3 2 4 2 2 3 2 4 2 2 3 2 3 2 4 2 2 3 2 4 2 3 3 2 3 4 2 2 4 4 3 4 4 2 3 4 2 4 3 3 2 4 3 4 2 4 2 3 4 3 2 При заданном значении z порядок получения промежуточных чисел оборотов от nmin до nmax может быть различным и зависит от принятого порядка переключения групп в передачи. Порядок кинематического включения групп в передачи находит отражение в структурных формулах в развернутом виде. Из за большого объема этот материал размещен на нескольких страницах: 1. Домашний очаг.:. История:. Окружающий мир:.
Справочная информация.:.:.:.:.:. Техника.:. Образование и наука:. Предметы:.
Мир:.:. Бизнес и финансы:.:.:.
6.Расчет и проектирование привода главного движения 6.1 Исходные данные и требования Исходными данными для разработки коробки скоростей станка являются: 1.Мощность электродвигателя; 2.Передаточные отношения ременной передачи и зубчатых пар: ременной; реверсивного механизма; первой группы второй группы 3.Количество валов согласно кинематической схеме станка 4 приведенных на схеме 3.1. 13; 4.Количество зубчатых колёс и количество зубьев нарезанных на них приведены в таблице 4.1. На стр.19; 5.Количество и расположение электромагнитных муфт вместе с реверсивным механизмом приведены на кинематической схеме 3.1. Коробка скоростей должна удовлетворять ряду требований, таких как: min размеры коробки скоростей станка, соосность валов в коробке скоростей, обеспечение требуемой мощности шпинделя станка и обеспечение снятия тепловых и других деформаций шпинделя, обеспечение удобства в изготовлении всех деталей корпуса коробки скоростей, их технологичность в изготовлении, удобство в обслуживании, надежности и по возможности простоте и унификации отдельных узлов коробки скоростей. 6.2 Расчет крутящих моментов, действующих на валах и на шпинделе Мощность приводного электродвигателя в металлорежущих станках расходуется на процесс резания (полезная нагрузка) и силы сопротивления (потери), возникающие в кинематических парах привода. Все потери можно разделить на постоянные, возникающие в режиме вспомогательного хода, и переменные, сопровождающие передачу полезной нагрузки.
При выборе мощности приводного электродвигателя потери во всей кинематической цепи принято учитывать общим коэффициентом полезного действия n общ. Величина n общ снижается в основном с увеличением потерь вспомогательного хода при возрастании скорости. Поэтому для приводов главного движения желательно, чтобы во всем диапазоне R n обеспечивалось постоянство передаваемой мощности. Потребляемая на резание мощность называется эффективной мощностью ( N е), которая выступает в качестве полезной нагрузки. Она связана с крутящим моментом на шпинделе М шп Исходя из условий полного использования мощности электродвигателя, определяем крутящие моменты M i на каждом валу коробки скоростей. Крутящий момент на валу электродвигателя определяется по формуле: где М эд. – крутящий момент на валу электродвигателя; N – мощность электродвигателя (кВт); n эд.
– обороты вала электродвигателя (об/мин); Крутящий момент на реверсивном валу (нулевой вал I 0) определяется по формуле: где М 0 – момент на реверсивном валу ( I 0),; М эд. – крутящий момент на валу электродвигателя; i p – передаточное отношение ременной передачи - КПД ременной передачи,; - КПД подшипника,; - КПД зубчатой передачи,. Определим крутящие моменты на валах коробки скоростей: где М i. – крутящий момент на данномом валу; М i -1 – крутящий момент на предыдущем валу; I i – передаточное отношение зубчатой пары; - КПД подшипников качения,; - КПД зубчатой передачи,. 6.3 Предварительный расчет диаметров валов и шпинделя Т.к. Основные размеры коробки скоростей ещё не определены (т.е. Опоры, расстояние между ними и т.п.) и следовательно нет возможности определить изгибающие моменты, поэтому расчет валов можно лишь вести приближенно, а именно на кручение по формуле: где М i.
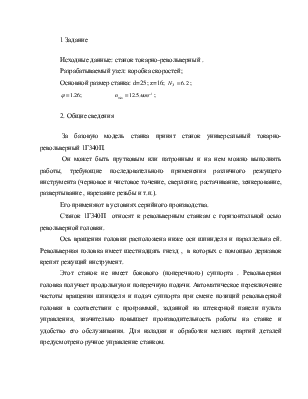
– крутящий момент на i-ом валу: - допустимое напряжение при кручении: По конструктивным соображениям полученные значения диаметров валов округляем до ближайших стандартных значений по ГОСТ 6636-84. Вал I 0 является шпоночным, для него выбираем диаметр 24 мм; вал I – шлицевой для него выбираем диаметр 23 мм; для лицевого вала II диаметр выбираем равный 23мм; для шпоночного вала III выбираем диаметр 60 мм. 6.4 Расчет модулей и параметров зубчатых передач Зубчатые колеса являются основным видом передач коробок скоростей, и от их габаритов и качества выполнения во многом зависят размеры и эксплуатационные характеристики всей коробки скоростей. Для определения модуля зубчатых колес будем пользоваться формулой: где m i – модуль i -той группы; K m – коэффициент прямозубых колес (К т=14); M kpi – крутящий момент на данном валу; - коэффициент учитывающий неравномерность нагрузки по длине зуба; Y F – коэффициент учитывающий число зубьев шестерни ( Y F =3.5); Z i – min число зубьев шестерни данной группы; - коэффициент ширины зуба; - допустимое напряжение материала После определения модулей рассчитываем геометрические параметры зубчатой передачи. Определяем межосевое расстояние в каждой группе передач, определяем делительный диаметр зубчатых колес, определяем диаметры вершин зубьев и диаметры впадин. Межосевое расстояние определяется по формуле: где A i – межосевое расстояние данной группы; m i– модуль данной группы; Z i 1, Z i 2– число зубьев данной группы.
6.1 Геометрические параметры зубчатого колеса где, z i – числа зубьев зубчатых колёс коробки скоростей; d i – делительный диаметр зубчатого колеса данной группы; d ai – диаметр вершин зубьев данной группы; d fi – диаметр впадин зубьев данной группы; b i – ширина зубчатого венца данной группы; l ст – длина ступицы; d ст – диаметр ступицы; S – ширина торцов зубчатого венца; Делительный диаметр определяется по формуле.